We will now take a look at the finishes and coatings of a sword blade. There are a number of different finishes that can be used or put on a blade: mirror finish, glossy finish, satin finish, bead blast finish, and various methods of bluing and coatings. Top custom knife maker Jay Fisher writes “Most makers simply don’t have the patience to execute a fine finish. Factories and manufacturers never properly finish a blade or metal fittings and components of the knife, ever.” Let’s learn more about the types of finishes for BJD.
Blade Finishes and Coatings
Mirror Finish
The most expensive finish is the perfect “mirror finish” you may see on expensive custom knives by top custom knife makers. It cannot be achieved by a polishing machine and must be done by hand. It takes a very high degree of skill and patience. The process involves 10 to 13 steps (depending on how you define them), working with progressively finer grits. If there are any scratches, the knife maker needs to go back and repeat starting with the step that should have knocked out a scratch of that size. It almost invariably requires an American or European sense of quality control to catch every scratch. This quality work can add $1,000 or more to a sword and is the main reason U.S. made custom Butterfly Swords usually cost over $3,000. Some steels are extremely difficult or impossible to bring to a clean mirror finish.
The chief advantage of a perfect mirror finish, other than beauty, is that the finely polished surface better resists corrosion. A long piece of shiny sharp steel also has an intimidation factor. The disadvantage is that it shows every scratch. Few individuals have the skill to polish them out. Because mirror finish knives are so reflective, a photographer needs a light box offering diffuse light and reducing reflected images to shoot a good photo.
Glossy Finish
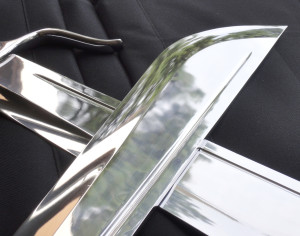
We define “glossy finish” as a high polish finish sufficient to provide a reflection. It is not the reflection of a glass bathroom mirror. We categorize most attempted production “mirror” finishes here, regardless of where made, including both low quality work and shiny work just a few fine scratches away from a perfect mirror finish.
Although Böhler 440C will take a mirror finish and the polishing on EWC’s lines is done by hand, no one can provide the finish of $3,000 or $4,000 pair of Butterfly Swords at production sword prices. EWC’s production run glossy finish is the best non-custom finish we have seen. There is a YouTube video of Master Wong repeatedly becoming entranced by his reflection in a pair of the Integral Knives to make the point.
Satin Finish
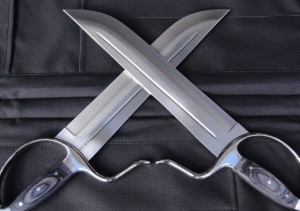
A “satin finish” consists of fine scratches lined up in the same direction to produce a low luster, non-reflective sheen. The steel looks like it has been brushed. The category allows for some scratches that look deeper than the others. That is the current satin finish offered by Randall Made Knives on their Sasquatch knives. D-2 generally looks best with a satin finish. Satin finished ordinary medium and high carbon steels, left unprotected, rust very quickly.
A lot of custom knife makers call a satin finish a “hand rubbed finish” and many knife collectors prefer it. It can be done quickly and requires far less effort and skill than a demanding mirror finish. Scratches and fingerprints are less visible on a satin finish.
A lower level of skill is required to remove scratches from a satin finish. It is also easier to photograph a Sifu holding the swords! The so-called mirror finish produced on a polishing machine or by insufficiently skilled labor – work generally done overseas due to cheaper labor — may look more like a satin finish.
Bead Blast Finish
A “bead blast finish” is achieved by pressure blasting a satin finish with an abrasive material like bead or sand to create a uniformly rough, non-reflective surface. The texture is more susceptible to corrosion than a finer finish but if you pick a steel that naturally resists corrosion such as high quality 440C and use a modicum of common sense it is not a problem. Bead blasted 440C is outstanding for a knife used in a military environment as is satin finish D-2.
Coatings
The best coating or blade treatment is none. There is no panacea besides using inherently corrosion resistant steel, which is why most of EWC’s carbon steel offerings are made from expensive D-2.
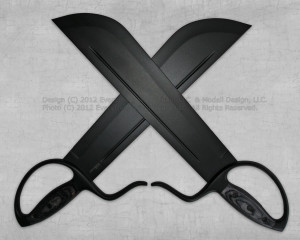
Coatings are used to make less expensive carbon steels palatable on ordinary carbon steel Western knives that should have used a quality stainless steel, on some of the rust-prone super steels, and to dull reflective surfaces in a military or law enforcement environment. They are also used to hide poor quality work from potential buyers. With swords and extremely long knives carbon steel can easily be the best or only steel for an anticipated use.
The first thing to remember is that all coatings and treatments may help prevent corrosion but cannot stop it since the cutting edge must be exposed and both wear down with use. They reduce the impact of sloppy maintenance but are not a license to forgo reasonable care. The next thing is that water or debris can slip between a coating and the steel and do more damage than if there were no coating. If you have a full tang product, the tang edges may or may not be coated. You must remain aware of the status of the coating or treatment and adjust maintenance accordingly.
The scariest coating is decorative chrome plating (which should be distinguished form industrial hard chrome). It guarantees the sword has the wrong steel, hides poor finishing, and chips and flakes off with time and use.
Powder coating is applied as a dry powder to a specially prepared surface then baked. It can be applied as a thin layer or used to create a thicker coating than possible with conventional liquid coatings. A thick powder coat will exhibit a textured surface. If the sole object for the blade is a smooth thin surface that will easily penetrate, a textured coating might not be the best idea. If the weapon has enough heft to do the job regardless (e.g., a Hudiedao) and the priority is reducing corrosion, you may prefer the initial wear limited to the higher area.
EWC uses a powder coat on many of its carbon steel products. It is an affordable technique used to help prevent rust. It will chip during steel on steel contact (including attempted extrication from a quillon trap) but is pretty good against wood. That said, the powder coat is not intended for use against any weapon or hard contact. Check out “TESTING BJD PROTOTYPES – SMASHING WOOD AND CONCRETE”, EWC Blog (Sept. 22, 2012), https://www.shopwingchun.com/testing-bjd-prototypes-smashing-wood-and-concrete/ (March 22, 2013) for more information and photographs.
Parkerizing is a treatment that can be used on carbon steel. It basically involves dipping the steel in a phosphate bath with zinc or manganese, inducing an electrochemical reaction. It is a simple and inexpensive process but not very helpful since the Parkerized surface further needs to be kept covered with a light oil coat or painted with an epoxy or molybdenum finish.
True bluing is used on guns to inhibit corrosion. The process is another electrochemical treatment, not a coating. It soaks into the steel. Done right it is extraordinarily beautiful. It can be done poorly, too. We have not seen it on a Butterfly Sword.
Titanium Nitride (TiN) is an extremely hard ceramic material that can be applied as an ultra-thin coating. The steel surface has to be specially treated prior to application. The coating is applied using a physical vapor deposition vacuum system. It comes in several colors and has the added advantage of providing a slippery surface. It has been called “pretty expensive” but the real problem is that the coating is regarded as fairly porous and not a good choice if the primary intention is corrosion resistance. There are a number of variations.
Several good high-end firearms coatings are also used on knives. These include KG™ Gun Kote, DuraCoat® and Cerakote™. They require meticulous pre-finishing consisting of cleaning and sandblasting with aluminum oxide. The coatings are then applied by spray. They generally come in air cure and/or bake dry versions. KG Gun Kote is a polyurethane resin. DuraCoat is a urethane. Cerakote is a polymer based liquid ceramic coating. Each product has its fervent supporters but independent testing commissioned by Cerakote showed the product superior to two competitors in a number of respects including corrosion resistance by a factor of 10. These methods or prohibitively expensive for production Butterfly Swords.
This video is Part 5 of 10 on Choosing Butterfly Swords by Jeffrey Modell. This video goes along with the blog article, but does not follow the exact same order of topics. We apologize that the AUDIO is OUT OF SYNC. This is the way the camera filmed the footage, so there is little we can do about it (simple aligning will not work). We hope you get some benefit, regardless:
[youtube]http://youtu.be/uVszNSoRwL8[/youtube]
Know enough about blade finishes? Click here to learn all about Wing Chun Swords Tangs, Handle Types, Alignment, Ergonomics, Handle Materials
One thought on “Choosing Wing Chun Butterfly Swords – Part 4 – Blade Finishes”